It’s time to talk titanium. This elemental metal has some profound properties that make it the go-to for folding knife handles, optics housings, and suppressors. But titanium is hard to produce, hell on tools, and requires so much more than steel or aluminum—and those extra elements are reflected in its precious price.
Is titanium worth it, or is it just hype?
Titanium isn’t rare. The element is everywhere. Unfortunately for us, though, it exists naturally in an oxide form that has to be refined to be useful as a raw material.
We’re talking guns and accessories here, folks, not aerospace applications. Obviously, titanium is worth all of the hassle for some industries. And I think there are some logical down-to-earth applications, too. But let’s start at the beginning.
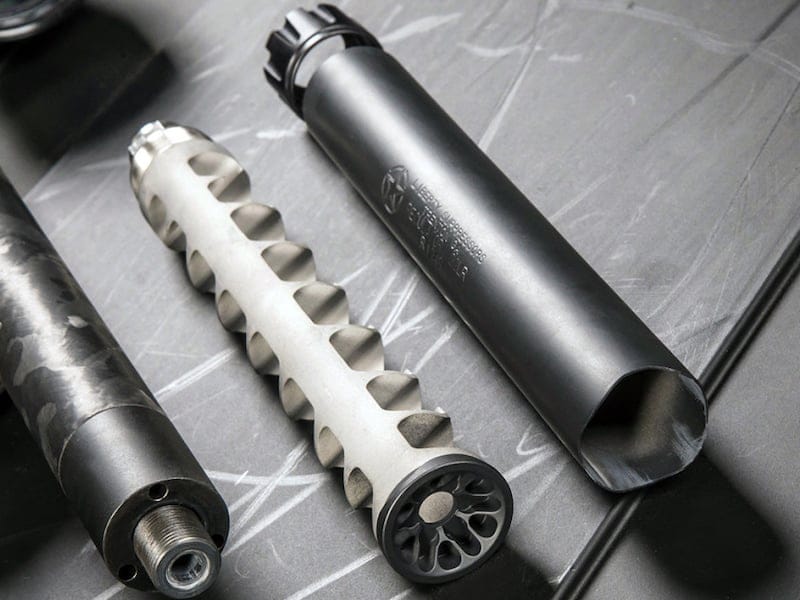
How is Ti made?
The oxidized form of titanium (titanium dioxide) must be worked under very exacting conditions to become billet or bar stock. The current favored method is the Kroll process.
The Kroll process heats the natural form of titanium dioxide to between 800 and 850 °C in a vacuum chamber. Chlorine is added, stripping out the oxygen and forming TiCl. Then, magnesium is added to strip out the chloride. The titanium forms a pure sponge-like structure that can be isolated.
Note: I have a Ph.D. in English. The last chemistry class I took was in high school, and I didn’t distinguish myself in that effort. I’m clearly paraphrasing the information above—and greatly simplifying what I’ve found in my research efforts.
This sponge is then crushed. The powder is melted, again in an oxygen-free environment, and is cooled into an ingot.
This complexity explains why there are no known examples of refined titanium that date before the reported discovery in the 19th century. This is complex.
Compare this to making steel—which I’ve actually done. Our ancestors built large, exceptionally hot fires and added iron ore. When it melted and pooled, they had iron. Working the iron repeatedly in a fire fueled by coke introduced carbon into the iron, and the end result, albeit accidental, was an early form of steel. It isn’t easy, but even lunkheads like me can do it.

Back to Titanium
So now we have a raw billet. What are its unique properties? Why, if steel is so easy to make, would anyone bother smelting Titanium?
The answer here is simple. Titanium is light. One cubic inch of Ti weighs just a bit more than a similarly sized cube of Aluminum. So weight is one factor.
Strength is the next. Ounce-for-ounce, titanium is almost twice as strong as aluminum. There’s a caveat here—the Ti we’re talking about in practical use (much like every other metal we use) is actually an alloy. Ti remains the primary ingredient, but other metals are added.
The third attribute of Ti is its high melting temperature, which is why NASA loves the material. It isn’t heavy but very strong, and its melting point is 1,668 °C (3,034 °F).
The easy way to think about Ti for the firearms industry is this oversimplification: Titanium is as light as aluminum but as strong as steel. A bonus for all involved is titanium’s natural corrosion resistance. What’s not to love?
Pitfalls of Titanium
So far, Ti is looking good. It conducts heat poorly (which is why it is used for ultralight backpacker mugs), but it is crazy strong and won’t rust.
But it is hell to work. Milling Ti requires really sharp tools. Dull cutting bits will gall the titanium and wreck the surface finish. This need for sharp tools increases the cost of working the material.
Ti is not as easy to heat-treat as steel, and it won’t register as high on the Rockwell Scale as some steel.
Titanium is hard to forge, as the material exhibits what’s known as “spring back,” which is exactly what it sounds like. This is great for some finished applications but bad if you need to forge or bend something to shape.
Welding with titanium is also complicated. Much like the smelting process, welding has to happen in an anaerobic environment or under a blanket of inert gases. Good welds are fantastic, but bad welds in titanium are uselessly brittle.

Using Titanium in Suppressors
For those following pop-culture events, Apple would like to sell you a titanium iPhone. Why? Beats me. Titanium must be cool.
It is great in suppressors. There are four dominant materials in suppressor builds today and titanium is one of the more premium choices.
A titanium suppressor is light, strong, and super resistant to heat and corrosion. These are good things. Titanium suppressors command a premium price, but their performance attributes are incredible.
The only downside is that titanium loses strength as it heats up. Some suppressors warn against full-auto fire (or prolonged sessions of fire in general), which is why most advertise titanium suppressors for hunting.
The other wiz-bang alloys are Inconel and Stellite. Both are nickel alloys. Cobalt, chromium, and iron are added to improve performance. The resulting material has outstanding heat tolerance. This, alone, is why Inconel is so often used in suppressors meant for high volumes of fire. But it is heavy, too.
Stainless steel is also a winner. While heavier, stainless steel is exceptionally strong, corrosion-resistant, and readily available, and it’s a solid choice for a general-use suppressor.
Need something strong and light for rimfire? Aluminum is a popular choice. This is easy to clean, super light, and affordable, but lacks strength. Don’t get it too hot, though.

Advances in Titanium design
As mentioned earlier, Ti is hard to work with. Cutting thin cones and tubes out of full billets or bars is ludicrous. And expensive.
Powder metallurgy, though, allows titanium to be cast into rough shapes that are close to the dimensions of the final product. The rough casting then needs only surface milling—not massive stock removal—to reach the final dimensions.
The use of powders allows for much more precisely measured alloy configurations, which means the finished product is more consistent. Both of these factors are cutting costs dramatically.
Understanding the numbers:
If you’re going to get technical about Ti, look at the grade. There are two common grades found in the firearms space: grade 5 and grade 9.
Grade 5 is 90% Ti, with 6% aluminum and 4% vanadium making up the remainder. This is super strong but much harder to work with than grade 9. Grade 5 will sometimes be noted as Ti-6-4.
Grade 9 has more Ti, only 3% Aluminum, and 2.5% Vanadium. While only half as strong as Grade 5, Grade 9 is much easier to work with.
Why don’t we see more titanium in guns?
Titanium Nitride is everywhere these days. The coating is applied as a surface finish, has a recognizable gold tone that some find attractive, and adds exceptional corrosion resistance to steel.
For example, if you own a Magnum Research Desert Eagle in 44 Remington, as we all do, you can spruce it up with a Titanium Gold Base 8-round Magazine.
Why aren’t guns made of Ti? It may have to do with the cost of the raw material and the cost of the machining. The forums are full of people talking about the possibilities, and it looks like some companies are experimenting with options, but nothing has caught on commercially.

Smith & Wesson makes some parts, like revolver cylinders, from titanium. They also use Scandium alloys, another super material, to build frames–but the barrels are still stainless.
Gun parts, though—like pins—exist. Lantac makes them, like this Titanium Pin Set for Gen 1-4 Glocks, and they appear to add a touch of bling.
Housings for optics, too, are being milled from Ti. Holosun has been using the material to great success. That seems logical for a pistol-mounted optic, like the HE508T-GR X2 Green Dot Open Reflex Sight, and makes even more sense for a hard-use rifle optic, like the HE515CT-RD Red Dot Sight.
Is that the future? Are we moving away from steel and aluminum? Titanium has its benefits, of course, and will likely become more common in applications once dominated by aluminum.
Steel, though, is not going anywhere.