Ian McCollum is back with an interesting and informative look at the World War II submachine gun that ultimately replaced the iconic Thompson in the US military’s arsenal. As Ian tells us, the Thompson was a great weapon, but it was very expensive and took a relatively long time to produce. With the US economy supplying the material to fight a global war, including supplying much of our allies’ needs, a cost-effective alternative had to be found. That alternative was the simple but reliable M3/M3A1 “Grease Gun.”
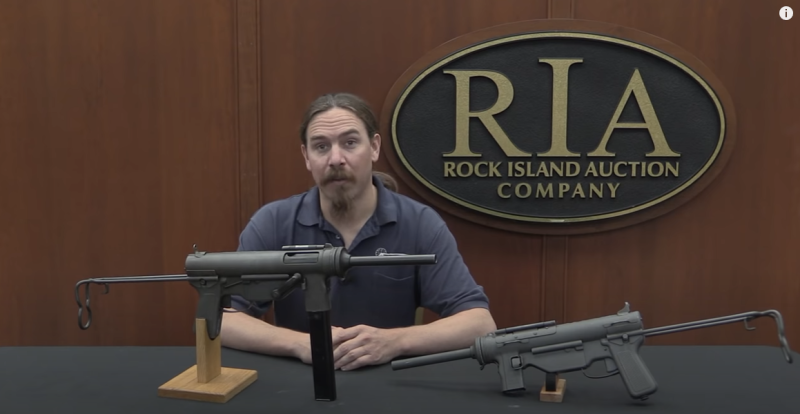
The problem with the Thompson was that it was made from forged steel and milled parts, which required craftsmen of a certain skill level and a time component beyond what wartime demands allowed. Even after being simplified to bring down the cost from $200 to $40 per unit, those craftsmen, and their machine tools, were needed for more important projects. Same with the forged steel. For instance, there were intense demands for every kind of engine. Think of all the land, water, and aerial vehicles that saw service in World War II and you’ll get an idea of how important that was.
An Economical Solution
So, in 1942, the Army Ordnance Board started looking for an alternative to the Thompson. In July of that year, a design submitted by firearms engineer George Hyde and industrial engineer Frederick W. Sampson was accepted as a prototype. Known as the T-20, the gun was tested at Aberdeen Proving Ground that fall and adopted as the “U.S. Submachine Gun, Caliber .45, M3” in January 1943.
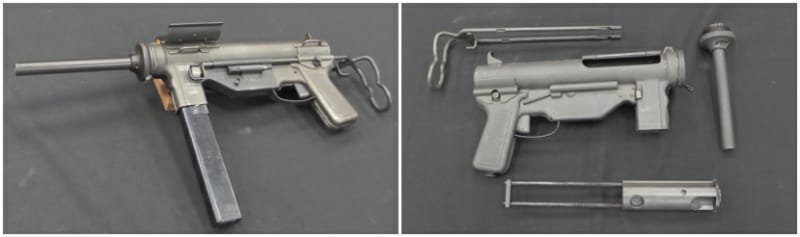
The contract was awarded to General Motors’ Guide Lamp division, which specialized in mass-producing stamped sheet metal components. In fact, Sampson’s contribution to the gun’s design was tailoring it to Guide Lamp’s capabilities, which were underused at that point in the war. In a testament to that efficiency, the first production M3s came off the line in May, a mere nine months after the Ordnance Department started the process.

Each gun cost $20.94 to build, about half what a simplified M1A1 Thompson cost, and it could be made in half the time with a 25 percent reduction in the necessary machine tools. That included the bolt, which was manufactured by the Buffalo Arms Company, the only component not made at Guide Lamp. The gun weighed about eight pounds, four pounds less than the Thompson, and its collapsible stock made it much more compact.

Quickly dubbed the “Grease Gun” because it looked like an auto mechanic’s tool of the same name, the M3 was attractive to Airborne and Amphibious Commands because of its reduced size and weight, as well as armored and service troops who needed smaller personal defense weapons due to lack of space. The M3 saw its first combat the next year in Normandy. Accustomed to their trusty Thompsons, soldiers didn’t like the Grease Gun at first, but it soon proved its worth in combat.

Not Pretty, But It Works
Compared to the Thompson, the M3 Grease Gun was an ugly duckling indeed. As Ian shows us, the gun consists of two stamped pieces of sheet steel crudely welded together to form the frame and receiver. The bolt and trigger assemblies, along with a sheet metal ejector, ride inside, and the barrel screws onto the front. A collapsible wire stock provides stability. It’s an incredibly simple, yet effective, design. The guns were Parkerized to protect them from the elements and the controls were rudimentary. Tolerances were deliberately generous to aid reliability in extreme conditions.

Thanks to those rudimentary controls, the gun was also simple to operate. It used double stack single feed stick magazines and fired from the open bolt. There was no safety, but the dust cover had an attached lug that slotted into a hole on the bolt that prevented firing when the cover was closed. The lug worked with the bolt open or closed. Just flip up the cover and the gun was ready to operate. A right-side mounted charging lever cocked the gun and opened the dust cover if it was closed.

The barrel was attached to a threaded adapter on the receiver and was easily removed for cleaning or storage. The bolt was mounted on two guide rods and operated freely within the cylindrical upper part of the receiver. Just unscrew the barrel and the entire bolt assembly slid right out. The original M3 version had an oil bottle attached to the left side and the welded-on sling attachments were compatible with the M-1 Carbine sling.
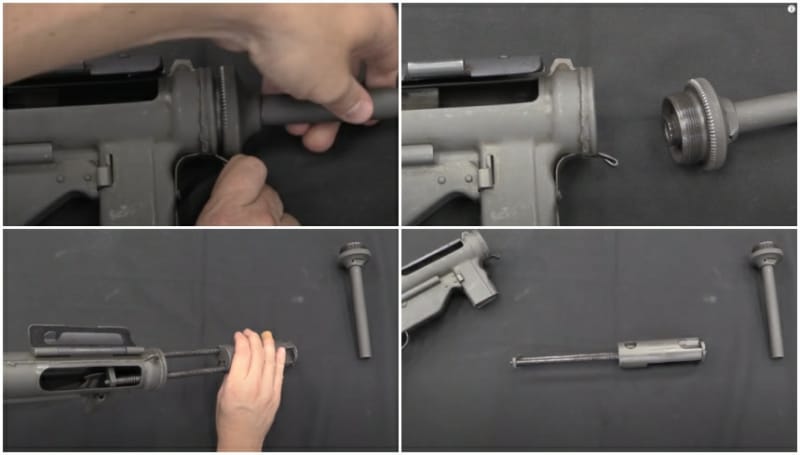
The M3, like the Thompson, was chambered in .45 ACP and was fired at the relatively slow rate of 450 rounds per minute. This made the gun more controllable and, even though it had no semi-automatic mode, made it possible to fire short bursts or even single shots once the soldier got used to the trigger. The slow rate of fire also helped new soldiers who didn’t have years of training under their belts quickly learn how to effectively use the gun.
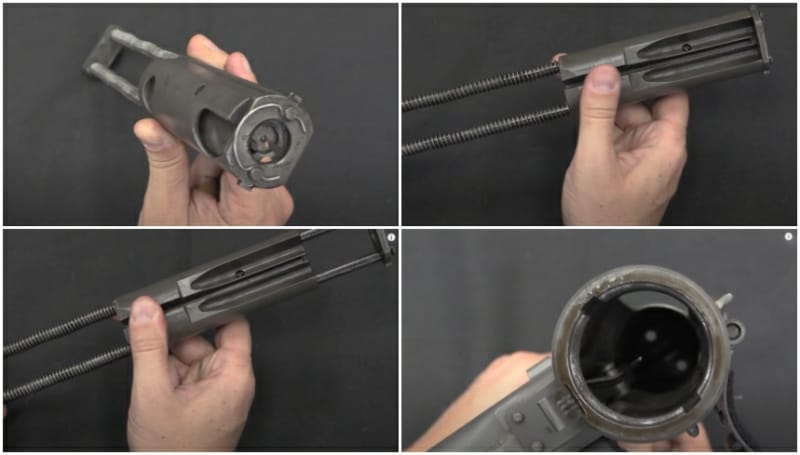
The M3A1: Solving a Few Problems
As with any new design, the Grease Gun had a few hiccups. The most prominent, and most concerning, was the propensity of the charging lever to break if the gun was dropped or banged around, rendering the gun inoperable. The lack of replacement parts prompted an interesting and effective field repair in which ordnance units cut a slot in the top of the receiver and welded a crude charging handle directly onto the bolt.
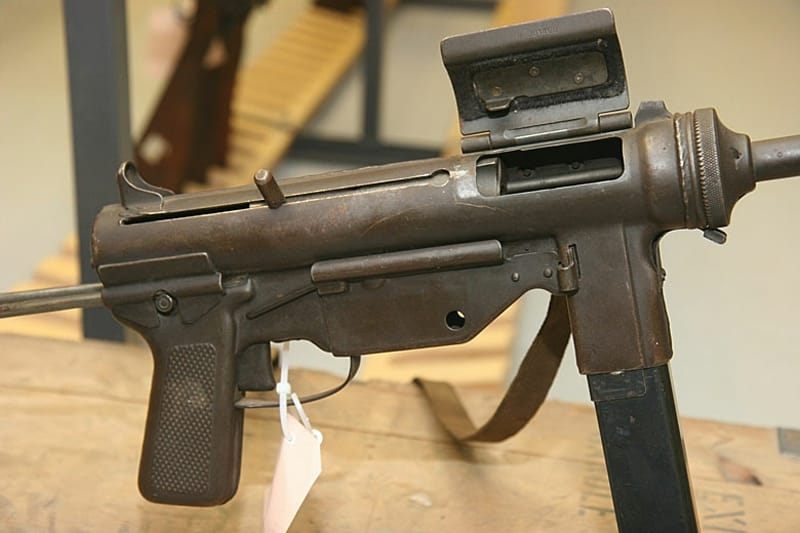
The charging handle issue, as well as a few smaller problems, were addressed in the simplified M3A1, which was standardized in late December 1944. The charging handle was eliminated entirely. It was replaced by a finger hole machined into the bolt itself by which the gun was easily cocked. This necessitated a larger ejection port, but that was a small concern and easily accommodated.
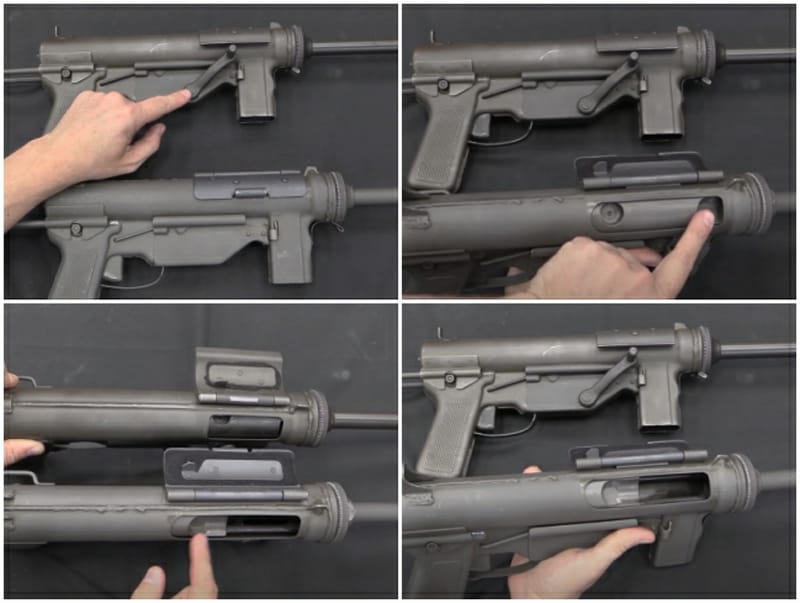
The rear sight, which had a tendency to bend if the gun was dropped just right, was strengthened with side support ribs, The side-mounted oil bottle was replaced with a larger, better-designed screw-in bottle that rode in the pistol grip. A magazine loading tool was attached to the wire stock, which could also now be used as a barrel wrench with the addition of two cutouts on the barrel nut.
One problem that was not fixed was an occasional tendency to jam. The magazine was based on the notoriously jam-prone STEN gun. The feed lips were not as sturdy as they might have been, often causing feed problems for the gun which, as a single feed design, had feeding problems to begin with. The British mitigated their jamming problems a bit by downloading their 32 round magazines to 30. Being chambered in .45 ACP instead of 9mm, the M3 Grease Gun had 30 round mags instead of 32. Ian mentions that most of the feeding problems of the Grease Gun were due to the mags but he doesn’t address any measures to fix the problem, nor did I run across any in my research other than the need to try to keep the feed lips from bending. US troops may well have downloaded the Grease Gun mags too.

Good Service
The M3A1 was a real improvement in the Grease Guns design, but it came so late in the war that very few actually made it to the front lines. Almost all the Grease Guns that saw combat in World War II were the original M3s. In all, 606,694 M3s and 15,469 M3A1s were built during the war. Despite “officially” replacing the Thompson as the front line American submachine gun in early 1945, there were never enough Grease Guns available for that to happen in reality. The Thompson was manufactured in lower numbers and remained in service until the late 1950s. A few even turned up in Vietnam.

The Grease Gun served long and well, remaining in official US service until 1992 with armored troops and truck drivers. It’s still used by several countries around the world and supposedly saw some combat in Iraq and Afghanistan. Not bad for an emergency-measure gun born from the economic realities of total war. Give the video a watch. The elegant simplicity, combined with obviously crude manufacturing methods is fascinating and Ian, as always, delivers a good breakdown. Even today, Ian says, the Grease Gun is “A very comfortable, efficient, effective submachine gun.”—
